The fixed hollow shafts ultrasonic detecting machine (HAT-M05 Model) is to detect the defect of wheel hollow shaft in alight state. It can detect the lateral and vertical detect of the axles outside surface and the shafts inside defect based on the regulations. When working with the customized feeler lever and the detecting module, it is able to detect the lateral defect of the axle inner surface. Integrated stopping wheel, lifting wheel and pulling wheel suit for all the EMU series rolling stock, it is domestic initiative.
1.Strong equipment compatibility
HAT-M05 Model which is compatible to all the current hollow shafts, like EMU1, EMU2, EMU2C, EMU380A/L, EMU3C, EMU380B/L, EMU5, covers a lot. Meanwhile, it is compatible to some domestic rolling stock hollow shafts, such as Lanjian and Xianfeng. The inner diameter detection range of the hollow shaft is from 30mm to 110mm.
2.High detection accuracy
System detection sensitivity 30-110mm
Circumferential defect≥1mm depth equivalent
Vertical defect≥2mm depth equivalent
Internal volume defect≥Φ2mm flat bottom hole equivalent
Maximum lateral defect sensitivity 0.5mm depth equivalent (when crack length≥10mm)
3.Convenient to operate & easy to use
The equipment uses a mechanical arm to drive the feeding mechanism. Operators only need to rotate the direction to finish the movement. It is really convenient to operate.
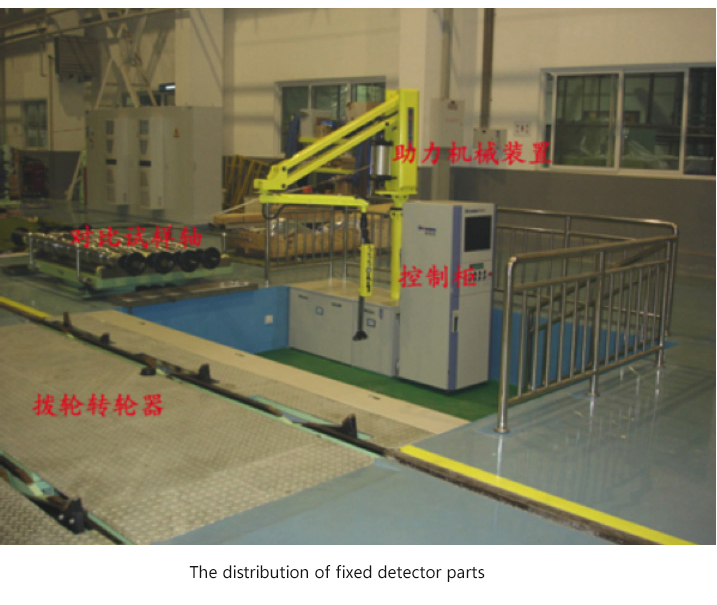
Mechanical power arm adopts pneumatic drive which is convenient to adjust, secured and reliable. After adjusting, you only need to turn on the switch. It does not need too much worker's operation. The wheel walks in from the input side and goes along cleaning position, detecting position and the oil applying position, then reaches the output side. The wheel movement is controlled by button pressing.
4.Complete localization of core components
The core components of the detecting equipment (ultrasonic controller, feeler lever system, control units) are developed by CHSR independently. The equipment has been produced locally which ensures operation, detection and maintenance of the equipment and it is out of the restrictions from overseas supplier.
Eight-channel ultrasonic controller is developed to detect the hollow shaft based on hollow shaft ultrasonic detecting characteristics. Adopting multi-CPU technology, huge storage technology, real time compression technology and high speed TGC compensation technology based on FPGA, it successfully solve the problems of highly synchronized hollow shaft ultrasonic detecting and massive data processing. It has improved the detecting efficiency while ensuring detection quality. Single axle detecting will be within 5 minutes. It is able to transmit all data to upper monitor in real time and reflect the true reliable fatigue damage degree of the entire axle.
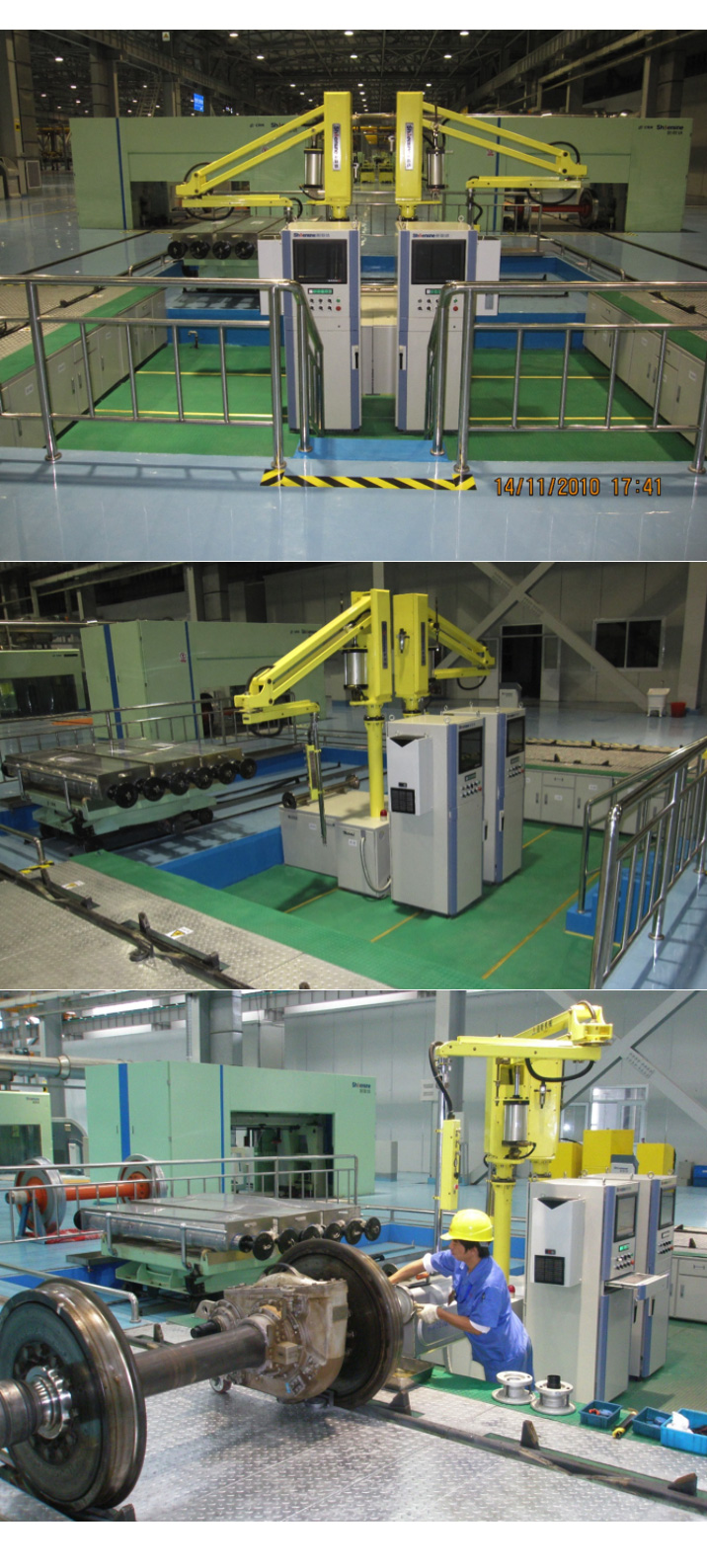